Pills and Pixels: Simplifying Medicine with Automated Prescription Filling

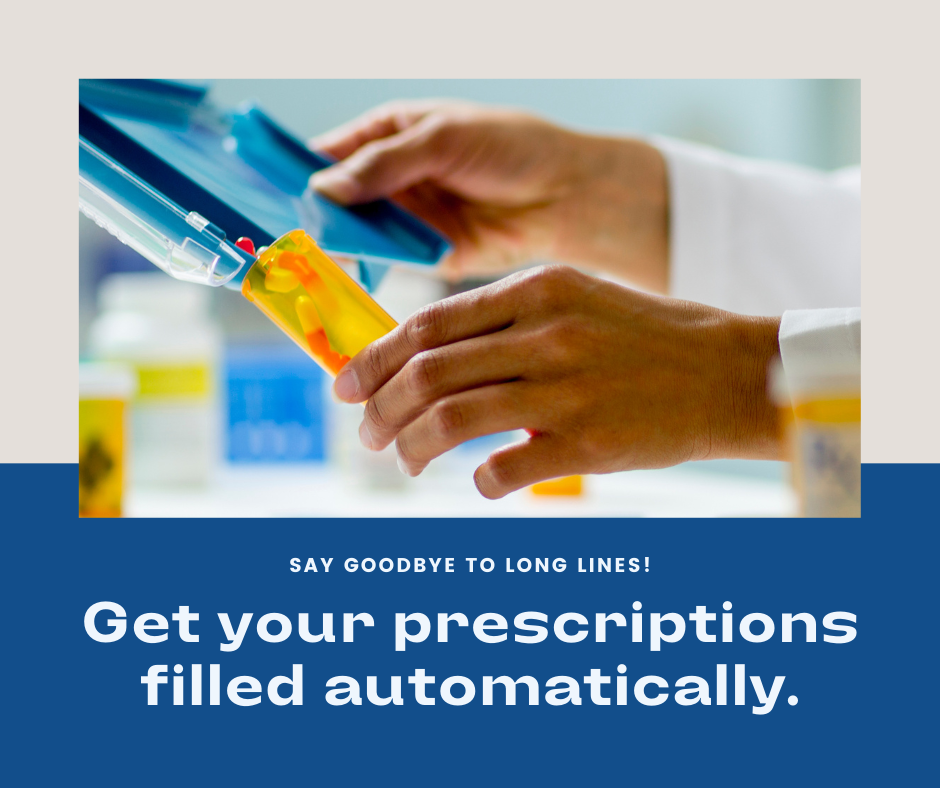
Understanding the Automated Prescription Filling Process:
-
The Journey Begins: Streamlined Data Input
What Happens: The automated prescription filling process kicks off when a doctor sends a prescription electronically to the pharmacy, or a patient submits a physical prescription that the pharmacy staff then enters into the system. This digital entry marks the prescription’s first step into an intricate, highly efficient process.
The Impact: Consider the precision of digital communication systems, which virtually eliminate the errors common in manual transmissions. A report by the Center for Information Technology Leadership estimated that electronic prescribing systems could prevent up to 85% of medication errors. This initial step ensures that every detail, from the drug’s name to the dosage and frequency, is accurately captured in the pharmacy’s digital system.
-
The Safety Net: Integration with Medical Records
What Happens: Once the prescription is digitized, it’s automatically cross-referenced with the patient’s electronic health records (EHR). This step is crucial for identifying potential drug interactions, allergies, or other contraindications that could harm the patient.
The Impact: Imagine a scenario where a patient, let’s call her Emily, is allergic to a specific medication, but that detail might have been overlooked in a manual check. The automated system instantly flags this allergy, preventing a potentially dangerous situation. Studies have shown that integrating prescription systems with EHR can reduce adverse drug events significantly, making medication safer for patients like Emily.
The Heart of Automation: The Automated System Springs into Action
What Happens: Sophisticated algorithms then take over to validate the prescription against the patient’s medical history in real-time. This step checks for dosage accuracy, drug interactions, and adherence to treatment guidelines.
The Impact: It’s akin to a highly advanced, real-time data analysis system that can detect anomalies in vast datasets within seconds. Pharmacies report a drastic reduction in dispensing errors, with some noting a 70% decrease in mistakes, ensuring patients receive the right medication at the right dose.
Optimized Inventory Management
What Happens: The system automatically checks if the prescribed medication is in stock, managing the pharmacy’s inventory efficiently. If a drug is running low, the system can prompt reordering, ensuring that essential medications are always available.
The Impact: This is similar to just-in-time inventory practices used in manufacturing, which have been shown to reduce waste and increase efficiency. For pharmacies, this means improved service to patients, with medications readily available when they are needed, minimizing wait times and avoiding treatment delays.
Precision and Safety in Dispensing
What Happens: The automated dispensing technology accurately counts pills or measures liquids, ensuring that patients receive the exact dosage prescribed by their healthcare provider.
The Impact: Think of this precision like a highly skilled chef measuring ingredients to ensure the perfect flavor balance. In pharmacy terms, it translates to patients receiving the correct amount of medication, crucial for the efficacy of their treatment. Errors in dosage can lead to ineffective treatment or adverse reactions, but automation reduces this risk significantly.
Secure Packaging and Labeling
What Happens: Once the medication is dispensed, it’s securely packaged and labeled with the patient’s name, medication name, dosage instructions, and any necessary warnings.
The Impact: This meticulous approach is akin to the careful packaging of consumer electronics, where every component, from the device to the instruction manual, is clearly and securely packaged. In the pharmacy, such labeling ensures that patients understand how to take their medication correctly, enhancing safety and efficacy.
The Human Touch: Pharmacist Oversight
What Happens: Despite the advanced automation, a pharmacist conducts a final review of the prescription before it’s handed over to the patient. This step ensures that the automated processes have correctly interpreted and filled the prescription.
The Impact: This is comparable to a pilot manually checking the autopilot settings before takeoff. Even with the most advanced systems, human expertise is irreplaceable for ensuring safety and accuracy. Pharmacists bring a critical layer of oversight, using their knowledge and experience to catch any potential issues before they reach the patient.
“Automation is cost-effective and provides a layer of predictability that can streamline processes and improve overall efficiency.” – Bill Gates
Why It’s a Game Changer
- Safety and Accuracy: By minimizing human intervention, automated prescription filling significantly reduces the margin for error. This proactive approach enhances patient safety by virtually eliminating instances of incorrect dosage or medication mix-ups.
- Efficiency: The streamlined workflow facilitated by automation expedites the prescription filling process. What once might have taken hours can now be accomplished within minutes, enhancing overall efficiency and convenience for both patients and pharmacy staff.
- Pharmacist Availability: With the burden of routine tasks alleviated, pharmacists can redirect their focus towards providing personalized care to patients. This shift fosters deeper interactions, allowing pharmacists to address inquiries, offer medication counseling, and provide invaluable support tailored to individual needs. Ultimately, it cultivates a more patient-centric healthcare experience, where attention to detail and empathy reign supreme.
Conclusion: The Future of Pharmacy
The automated prescription filling process embodies the integration of technology and healthcare, aiming to improve patient outcomes, enhance safety, and streamline pharmacy operations. Through each step of this process, from initial data input to the final pharmacist check, automation plays a pivotal role in ensuring that patients receive the right medication, at the right time, in the right dose. This technological advancement not only represents a significant leap forward for pharmacies but also marks an evolution in the broader landscape of healthcare, where precision, efficiency, and patient safety are paramount.
Comments Section:
We’d love to hear your thoughts! How do you feel about the integration of technology in healthcare, specifically in pharmacies? Share your experiences or any concerns you might have below.
Keywords:
Automated Prescription Filling, Pharmacy Technology, Healthcare Innovation, Medication Safety, Pharmacy Efficiency
Recent Comments